
Features Overview
The Titanium Explorer Series of Auto Gyrocopters have a range of impressive and handy features designed to help you with flying and storage.
Fuel Tank
Fuel Tank
Here at TAG the most important thing is safety so when it came to designing the fuel tank we looked for the best material possible.
This happened to be:
High-Density Cross linked Polyethylene (XLPE)
High-density cross linked polyethylene, or XLPE, is a thermoset resin that is specifically designed for critical applications like chemical storage and fuel tanks.
During the XLPE manufacturing process, a catalyst (peroxide) is built into the resin, which creates a free radical. The free radical generates the cross linking of the polymer chain, so the tank essentially becomes one giant molecule. The result is a resin that is specifically designed for critical chemical and fuel applications.
XLPE VS. Linear Polyethylene (HDPE)
- XLPE has 20 times the environmental stress crack resistance of HDPE.
- It has 10 times the molecular weight of HDPE.
- It has 5 times the impact and tensile strength of HDPE.

Titanium Frame
Titanium Frame
We decided to use Titanium for our frames because of its high strength-to- weight ratio.
It is a strong metal with low density that is quite ductile All the welds on our frames are heat treated after welding.
The heat treating process take 5 to 6 days to complete, takes 2 days to heat the oven up to around 500 degrees and then holds that temperature for 2 days before cooling it down, all in a vacuum and zero oxygen environment.
This makes our Titanium frames the only Gyro copter frames in the world of any material to be correctly heat treated to de-stress the welding.
Bolted frame
Our frame is built is 3 sections and bolted together using 5mm Gr 5 Titanium plates and crush tubes. This eliminates the possibility of cracking around the mast.

Fuselage & Tail Design
Fuselage & Tail Design
The Fuselage and tail are made from carbon fibre and honeycomb construction and vacuum formed into the mould.
This allows for a very strong but very light construction.
One of the problems in tandem gyros is the amount of air that is forced into the rear seat area making it unpleasant for the passenger.
We spent many hours with our design team using 3D wind tunnel technology to overcome this problem.
With the air travelling evenly around and over our large front windscreen compared to other tandems where the air flow tends to travel around the side of the windscreen and very little over the top, this compresses the air as it travels around the side of the screen thus forcing it back into the rear seat compartment.
The Titanium Explorer has minimal air being drawn into the rear seat compartment.

Hub Bar
Hub Bar
With reports of cracking Aluminium hub bars and cracking aluminium rotor blades on some gyros we decided to look at better materials to use in our new gyro.
We worked with the Australian defence force academy who had done studies on cracks in gyrocopter Aluminium hub bars and were continuing their studies on making hub bars from composite materials.
While we found this to be a very strong and most suitable for the purpose it was very labour intensive which increased the cost to an unaffordable amount.
We then looked at replacing the Aluminium hub bar with Aerospace grade 5 Titanium and use it in the vertical axis to overcome the cracking issue as safety is our number one priority.
Titanium is very resistant to cracking and doesn’t rust or corrode and is up to 5 times the yield strength of Aluminium and many other metals.
TAG Aviation Pty Ltd has received an exemption from ASRA on AD 2008.01. on xray and eddy current testing of hub bars at 500 hours.
Nose Wheel
Nose Wheel/SUSPENSION
Before starting the design on the Titanium Explorer we spent a lot of time talking to customers and gyro enthusiasts about the types of improvements they would like in a newly designed gyro.
Constantly expressed to us as a common issue was a suspension nose wheel. Because of rough airstrips and taxi ways on many country airfields in Australia our design team spent many hours on 3D design to create a full suspension nose wheel with integrated rubber dampeners to generate a comfortable and practical suspension system.
The unit is fabricated from cast aluminium with a 30mm Titanium shaft that has been precision machined to fit the hub assembly, this makes it extremely strong and removes the need for additional fasteners.
The front nose wheel also allows for a tight turning circle however the ratios are designed in such a way that the normal rudder movement both in flight and on landing do not allow the nose wheel to turn to its full lock position, to turn tightly you need to push the pedal further.
Rear Suspension
The rear suspension also contributes to this smooth ride as it is designed to absorb the bumps in both the vertical and the horizontal plain.
The rear suspension is made from 7000 series aluminium which works extremely well on rough runways and is complimented by the rubber block suspension on the front.
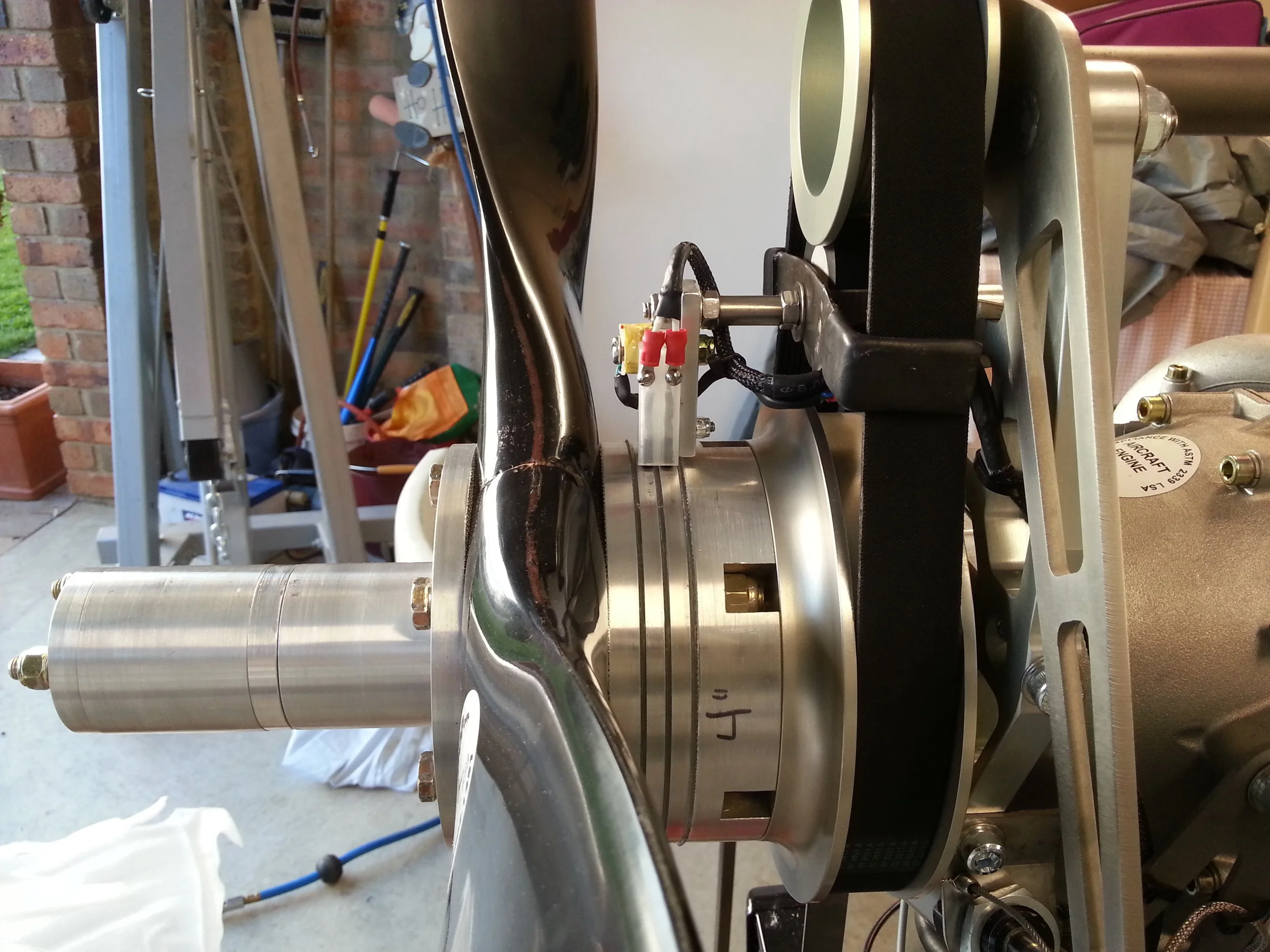
Powerful Pre-Rotor System
POWERFUL PRE ROTOR SYSTEM
We designed a pre-rotor system that is simple to keep the pilot in complete control at all times. It is designed so the pilot can control the spin up speed of the rotors to reduce overstress of the system
Designed as an open system, in turn overcoming the problems of blockages in the air valves from dust and moisture. Runs extremely quiet and is highly efficient.
We also have a manual pre rotor lever as a backup in case the primary pre-rotor system fails, additionally aids in aligning the rotor forward and aft on the ground.
The pre rotor system on the Titanium Explorer is capable of spinning the rotors up to over 300 RPM(not recommended)

Rotor Blades
Rotor Blades
Over the past 30 years most helicopter companies have gone back to making full composite rotor blades and rotor blade hubs, the main reason for this is because of fatigue affecting rotor blades made from aluminium.
Unfortunately there have been recent reports of a number of aluminium rotor blades developing cracks in gyro copters.
Composite rotor blades usually have an extended life, don't suffer from fatigue (provided they don’t get physically damaged) and are generally much smoother in-flight. This is because composite rotor blades if designed correctly can flex in-flight absorbing a lot of loads and reducing the teetering on the hub bar.
We decided to build the strongest and safest rotor blades ever built for gyro copters with the help of some of the world's leading aerospace composite engineers, with their extensive knowledge in helicopter rotor blades we were able to develop a rotor spar that is as strong as those used in helicopters.
Our composite rotor blades we developed for the Titanium Explorer are made from pre-preg carbon fibre, "Prepreg" is the common term for a reinforcing fabric which has been pre-impregnated with a resin system.
This resin system (typically epoxy) already includes the proper curing agent. As a result, the prepreg is ready to lay into the mould without the addition of any more resin. In order for the laminate to cure, it is necessary to use a combination of pressure and heat.
There are several advantages to using a prepreg rather than using traditional hand layup.
Maximum strength properties. In a hand layup, it is difficult to achieve 50% resin content. This means that the finished laminate weight is 50% fabric and 50% resin. Typical hand laminates, even when vacuum bagged, end up with a significant amount of excess resin. Excess resin increases brittleness and reduces overall properties. On the other hand, most prepregs contain around 35% resin. This is ideal for maximum cured properties and generally impossible to achieve in normal hand lamination.
With prepreg carbon fibre the TG (which is the point at which resin starts to soften) is around 120 degrees Celsius compared to wet laid composite that has a TG of between 65 to 85 degrees, so for the first time ever you could have pure black composite rotor blades.

Rotor Head
Rotor Head
Our rotor head is made from Grade 5 Titanium with a strength greater than 1000 mpa, this makes our rotor head the strongest in the world and a first using titanium.
The rotor tower is designed with strength and safety in mind.
Starting with the main bearing axel made from 1045 high tensile steel and held into the rotor head with 2 AN bolt making it easy to remove and interchange with other Tag gyros without affecting the rotor balance, a brilliant innovation.
The teeter bearings have both roller and thrust bearings to take the load in all direction and are pressed into a threaded housing making rotor balance easy.
Warning System
Warning System
With the request from my dealer in New Zealand to develop an early warning system for low speed rotor flap after he had see several gyro accidents caused by absent minded pilots on another brand of gyro .
With the help of an electronics engineer we have now available for customers a plug in system to address this problem.

Storage
Storage
One thing we wanted was a good volume of storage so we designed 196 litres of storage into the side pods and another 22 litres in the rear console, if you don’t have the rear instruments.
Ideal for camping trips or going to air shows , with the long storage area enabling you to put long tent poles and fishing rods safely inside.

CNC Machining
CNC Machining
Here at TAG we use the latest in 5 axis CNC machining for all machined parts used in our aircraft.